Roel Gevaers (University of Antwerp): “Dry ice has potential to significantly influence cold chain”
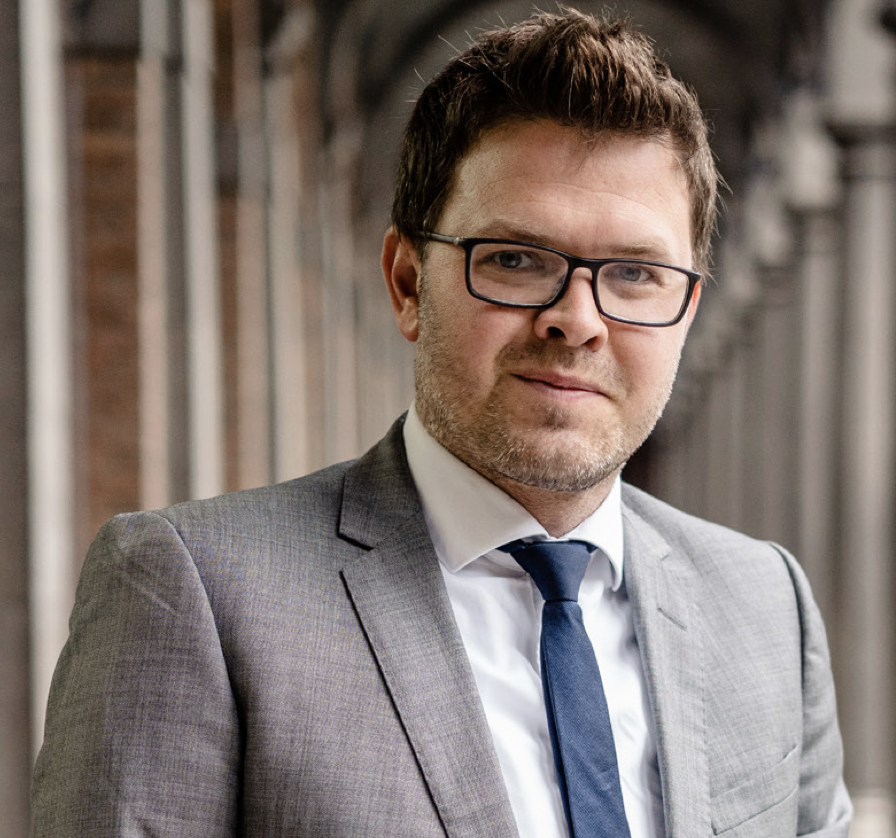
The cold chain faces major challenges, including in terms of sustainability and carbon footprint. Especially in the last mile, passive cooling with dry ice offers great opportunities to address them. However, dry ice is little used today. That is the conclusion of Naeem Salim Bagwan, Roel Gevaers and Wouter Dewulf of the University of Antwerp (supporting partner of Log!Ville). They published a paper showing that the potential of dry ice in the supply chain is still significantly underexposed. Professor Roel Gevaers explains the advantages and disadvantages of dry ice in refrigeration logistics.
Four years ago, dry ice came into focus because Pfizer’s Covid vaccines had to be transported in hermetically sealed cases at a temperature of -70°C. Synthetic dry ice was the best solution to ensure that temperature is constant.
Dry ice – a compressed, solid form of CO2 – was until then mainly used to store and transport medication or organs when mechanical cooling (active cooling) cannot be used. “After contacts with Cold Jet, a Belgian-American manufacturer of machines to produce dry ice (with Pfizer, among others, as a customer), we came to the observation that outside the pharmaceutical sector, the use of dry ice is still very scarce in logistics and transport. For example, it is put in a slide at the bottom of trolleys on board aircraft to cool them or still sometimes used in a separate compartment of a delivery van to take care of the last mile of frozen products, but not to transport refrigerated products. Therefore, we investigated the feasibility and sustainability of dry ice as a refrigerant in the supply chain,” says Roel Gevaers.
“Reducing CO2 and other greenhouse gas emissions is a big challenge in the transport and logistics sector and an even bigger one in the cold supply chain. It is possible that dry ice is a means of reducing those emissions. Therefore, we reviewed the published academic literature to know the extent of product awareness and use of dry ice in the cold supply chain. Our main finding is that there is very little research around that globally. In other words, the usefulness and benefits of dry ice are underestimated, especially in the distribution and last-mile cold supply chain,” he adds.
Advantages over active cooling and gel packs
During the covid crisis, e-commerce in the food industry grew tremendously. This trend is expected to continue, with the online food and beverage market growing at an average CAGR of 17.6% to USD 109.23 billion by 2026 with a CAGR of 17.6%. This increase will put tremendous pressure on the existing cold chain infrastructure, especially on the transportation segment that mainly relies on active cooling systems.
“These have the advantage of easy temperature control, but from the production site to the consumer they often face temperature fluctuations. This is even more the case in the last mile as doors are opened at each delivery so cold air is lost and warmer air enters. Especially during the summer months. These fluctuations – especially in pharma transport – can lead to product damage and even wastage. Another disadvantage is that most active cooling systems require large amounts of energy. Another disadvantage is that it is difficult to also transport ‘ambient’ products in a refrigerated van, so one has to use two different vans for the same round,” he lists. “In the last mile, passive cooling is therefore often used.”
“Today, the standard is a cardboard box containing an isomo box with gel packs that keep the food or pharmaceutical products cool. This is very efficient because thanks to the well-insulated packaging, products can be kept at temperature for up to 10 days, which even allows transports as far as Africa, for example. So this method is very convenient but also very polluting: after use, people usually throw away the isomo and gel packs. Evidently, gel packs are very difficult to recycle and ‘returning’ them is a very expensive and complex process. Dry ice is a particularly interesting alternative to gel packs because the CO2 is simply released as a gas after use (‘sublimating’). So there is no waste,” Roel Gevaers adds.
There are three ways to apply dry ice: one can put the ice in bags of, say, 30 by 10 by 5 cm (e.g. to cool the air in airline refrigerated trolleys), form cubes of 2 or 3 cm and scoop them directly onto the (frozen) product or use it as a loose substance – a kind of snow.
CO2 allocation
To make dry ice, people use CO2 that is released from industrial and chemical processes – for example, beer fermentation or ammonia production – and capture it. If one did not capture this CO2, it would end up in the atmosphere and contribute to global warming. With dry ice, although that CO2 also enters the atmosphere – albeit delayed – one avoids the CO2 emissions from refrigeration agglomerations. So the overall carbon footprint of dry ice is smaller than that of active cooling with diesel or petrol. “Our further research will aim to quantify that scientifically,” adds Roel Gevaers frankly.
“Further research will also be needed to allocate those CO2 emissions. That aspect is very important in the context of CO2 reporting. Today, there is no consensus whether to allocate those emissions to the factory where the CO2 is captured or to the supply chain. Colruyt, for example, conducted tests with refrigerated containers and dry ice, but stopped because the sublimation was assigned to transport. That is why UAntwerpen is working on a model to map and determine allocation,” he adds.
Impact on packaging
Asked whether increased use of dry ice as passive cooling will have an impact on packaging in the cold supply chain, Gevaers replies nuanced: “More insulating material is needed, preferably sustainable and not thrown away but reused. Then managing return flows is a challenge, which is actually a general concern, in the sense that the entire supply chain faces that challenge”.
Those packages will also be larger, because of the insulation material. That means that a van or truck can carry less payload. So more vehicles are needed to transport the same number of products. Again, he responds with nuance. “That is true, but one should not lose sight of the fact that both refrigerated and ‘ambient’ products are transported in the last mile. If you can combine both thanks to passive cooling, you can bring together two flows that would otherwise require two separate vans. So you potentially save many kilometres in total, further research will have to show.
Conclusion
According to Gevaers, dry ice has real potential in the cold chain and certainly in the last mile. Not only as a more sustainable alternative to polluting gel packs as passive cooling, but also for vehicles with active cooling. Fuel consumption decreases as no cooling aggregate is needed and food and medicine safety is better ensured as there are no temperature fluctuations.
Still, he sees some challenges that stand in the way of wider use of dry ice for now. “More research is still needed around the organisation of return flows, around CO2 allocation and around the CO2 balance against other methods of passive cooling and against active cooling. Within University of Antwerp, we are already working on an emissions calculator for active versus passive cooling. This is expected to be ready in March or April.
The paper by Naeem Salim Bagwan, Roel Gevaers and Wouter Dewulf can be downloaded here.