Dirk Torfs (Flanders Make): ‘Developing new technologies with other companies and then sharing them with others’
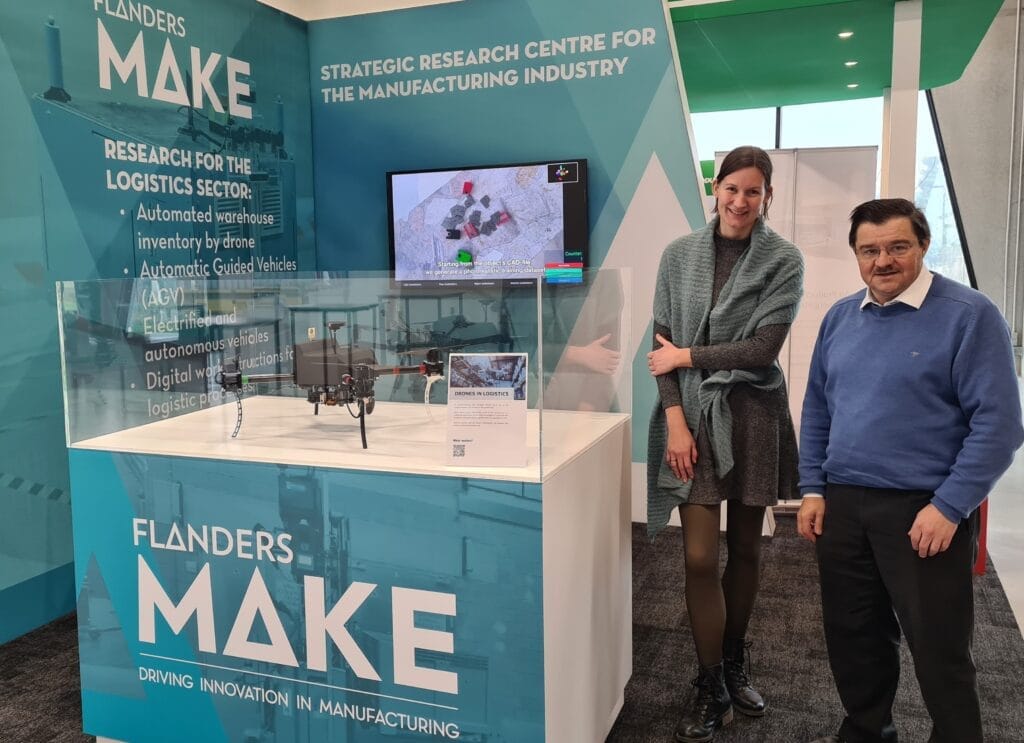
Flanders Make has recently become an Innovation Partner of Log!Ville. This strategic research centre for the manufacturing industry supports Flemish SMEs and large manufacturing companies to become more internationally competitive. ‘The focus lies on research and innovation to accelerate the development of Industry 4.0, where we allow various actors to cooperate within one ecosystem. Many innovations are also relevant to the logistics sector. Becoming a Log!Ville partner was an easy choice,’ explains CEO Dirk Torfs.
Flanders Make was founded in 2014 by combining the clusters Flanders Drive (car industry) and the Flanders Mechatronics Technology Centre (machines), in collaboration with several departments from all Flemish universities. On the basis of high-tech research and innovation, it offers active support to businesses in the manufacturing industry in developing and optimising their products and production processes.
Dirk Torfs: We bring researchers, businesses and governments together within an ecosystem which allows research and innovation to be accelerated and provides added value for all parties. Flanders Make functions like an orchestra conductor, uniting parties around innovation to strengthen the competitiveness of the businesses and guide them through Industry 4.0. To this end, we rely on approximately 800 experts, a quarter of whom are our researchers, while the other three-quarters are researchers connected to a university. The research and projects which we lead adopt a long-term vision and also take a very broad perspective on technology. Industry 4.0 is a transversal technology that is relevant to all sectors. That is why we unite researchers who are experts in various areas, both academics and specialists in applications, and let future trends set our strategy. Nevertheless, the environment remains easy to access. The government finances the research and this must, in turn, serve the purposes of the businesses.
Flanders Make started in the manufacturing industry. How was the scope expanded to cover logistics?
DT: Industry 4.0 does not stop with the manufacturing industry. It is not simply about making machinery work more efficiently but also about implementing new technologies such as error detection, artificial intelligence, digital twins, vision technologies, and much more. These could also be useful in other sectors, such as logistics. That is why we work closely with VIL; they understand the needs of the logistics sector which is highly diverse as well.
Almost every sector or industrial segment relies on logistics and this sector uses extremely diverse technologies which are closely connected to our original specialities, i.e. vehicles and machinery. AMRs (Autonomous Mobile Robots), for example, are vehicles which require accurate localisation and position determination, two domains in which we have a great deal of expertise. We also have know-how concerning vision technology and drones, which we have combined in order to use drones for inventory purposes within logistics and industrial settings.
Will you bring these developments to the market yourself?
DT: That is not our intention. We pool different competencies, based on the company’s specific needs, to create a working prototype. Depending on the Technology Readiness Level (TRL), the developed technology can be picked up by a business and implemented or, if necessary, further developed to be placed in the market. In other words, we bring researchers and developers together to create a workable concept for a business. Once we have demonstrated it can work, the business can take it further. Or another company can work on the technology to develop their own application.
Can you provide an example?
Researcher Ellen Van Nunen: Flemish companies produce around 16 million tons of primarily commercial waste every year. This waste ends up in different types of containers on the work floor which must then be collected. After a brainstorming session with a few members, VIL identified a need for the automation of this process. The waste management company Indaver was, in turn, looking for automation applications to optimise its collections from commercial sites.
Together with VIL and Indaver, we brought various parties together to realise a Proof of Concept for a system that could autonomously move waste containers. These parties included FT Group, a specialist in the automation of internal transport solutions; Pixelvision, an expert in vision technology; and the University of Antwerp with its specialisation in sonar technology.
Developing this type of concept is no mean feat. As well as the fact that various types of containers have to be picked up and moved, this autonomous solution must also work inside a building and outdoors, as full containers are often placed outside on the company’s site.
To tackle this challenge, we worked with artificial intelligence: AI algorithms can recognise containers in difficult weather conditions, such as rain, mist or snow. This is a regular task for Pixelvision. Flanders Make is working on ‘data augmentation’ techniques to train this type of AI. Based on these images, an AI network can, for example, learn what a container looks like in the rain. Together with new ultrasound technology that was developed by UAntwerpen, we were able to integrate a robust solution.
The autonomous mobile platform which moves the containers must also fulfil other requirements; it must also be able to move across less smooth surfaces, move lids on the containers, and so on. Together with FT Group, we analysed which design would probably be most favourable in terms of costs and robustness.
Once the basics had been set out in a Proof of Concept, other applications could also be elaborated. E.g. the Audi factory in Vorst asked for AMRs that could be used inside the factory as well as outdoors. The technology developed within the waste container project, about vision, localisation and driving skills, could be used for them too.
Who is the owner of the developed technology?
DT: If it is ‘one-to-one’, when we develop something for one company, they are the owners of the ‘intellectual property’. If it is ‘one-to-many’, when it is a generic project, the IP is owned by the participating development companies but also by us. Other companies can then use the technology under a licence.
Why did Flanders Make become an Innovation Partner of Log!Ville?
DT: Firstly, to demonstrate what we could mean to the logistics sector. Secondly, to create closer contacts with the sector across the board and not just with one company. Thirdly, to demonstrate the technology we already have. And lastly, because of the networking opportunities. We are only familiar with a small section of the logistics sector whereas VIL knows the whole sector. This gives us a much broader reach and allows us to inspire other companies and show them that there could be applications for them too.
On the other hand, we have the right connections with other technology providers and OEMs. It is great if you can unite the various parties and identify needs and establish how we can ensure these needs are fulfilled. That is a two-way street as well; added value elements move from Flanders Make to Log!Ville and also vice versa.
Could that lead to co-creation?
EVN: Definitely! That is our goal: develop new technological innovations with other companies and share the technology we already have with others so that we can have an impact and ensure Flanders not only stays competitive in terms of technological developments but also in terms of innovation.
Research and innovation are unknown to many people. What we increasingly try to do is use demonstrations to show companies that innovation does not just offer the potential for one particular sector but in other sectors too. If they can see our technology here, we hope that they will ask: ‘If you can do that here, could you perhaps do it for us too?’ This broader, more global outlook can, in turn, lead to new cooperative partnerships.
What does Flanders Make demonstrate at Log!Ville?
EVN: At our booth, we showcase two of the logistics demonstrators: our inventory drone that can count boxes on the racks in a warehouse and can localise products, and a robot arm with a Pickit camera, which can pick up items very effectively, as it is fitted with a vision system that can be trained quickly and efficiently using AI algorithms. It can recognise objects even in an unstructured environment.
This robot arm is a Proof of Concept. By demonstrating this at Log!Ville, we can reach out to visitors from companies and other partners who could use the technology in their own fields of application or develop it further, for example under a licence.
By the way, the vision technology that was developed for the drone can also be used in other ways, for example, it could be installed on a mast of an AMR or forklift truck.
With these two examples, we hope to demonstrate that the technology we are developing is reusable and can form the building blocks for other applications.
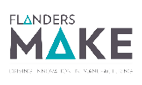