Hans Thibau (Atlas Copco): “Inspiration at Log!Ville leads to accelerated innovation”
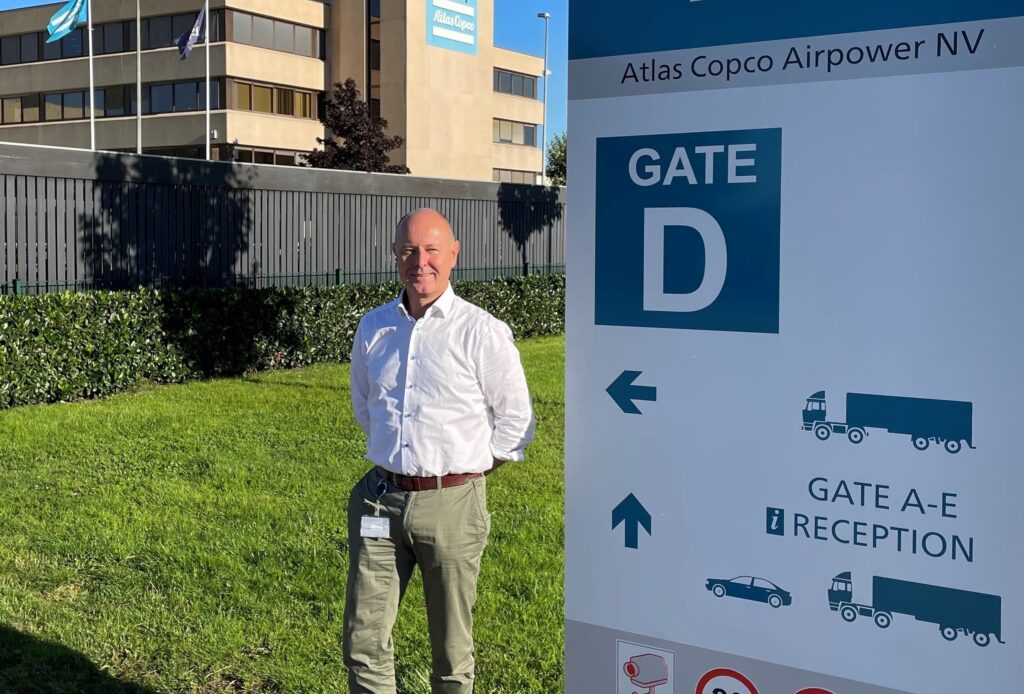
The heart of Atlas Copco’s operational business is not in Sweden, but in Belgium. Two of the Group’s four business areas, which together account for almost 60% of global sales, are headquartered in Antwerp: Compressor Technique and Power Technique. Antwerp and Hoeselt are home to the group’s two largest distribution centres. Antwerp takes care of Compressor Technique and Hoeselt all other business areas. They deliver worldwide. “Innovation – also in logistics – is one of Atlas Copco’s three core values. It was therefore logical for us to become Supporting Partner of Log!Ville,” says Hans Thibau, Vice-President Logistics Compressor Technique.
Everyone probably knows Atlas Copco Airpower’s buildings next to the A12 highway in Wilrijk. But many do not know the activities take place there. Can you say a bit more about it?
Wilrijk is Compressor Technique’s headquarters: it is our most advanced compressed air R&D excellence centre in the world. More than 3,000 employees ensure the daily development and production of compressors, dryers and filters, among others, here. The site also houses more than 200 IT workers and a global logistics centre. Power Technique’s headquarters is just steps away, but in a different municipality. The Atlas Copco Airpower site is therefore the world’s largest compressed air plant.
This prominent position worldwide was created 67 years ago with the acquisition of Belgian compressor manufacturer Arpic Engineering. Pour la petite histoire: that’s where Copco comes from in the group’s name: Compagnie Pneumatique Commerciale.
While stocks used to be located in the various factories, some 35 years ago the logistics of spare parts for compressors were centralised in a global distribution centre (GDC) in Wilrijk. Meanwhile, there are distribution centres in China, the US, India and Italy. But they are coordinated from here.
So logistics is a very important part of operations in Wilrijk?
Certainly: it is crucial for the operation of the compressor division factories located here, as well as for the distribution of maintenance components and spare parts to sites and customers worldwide.
Inbound, we call on Katoen Natie to organise the supply of components to the on-site factories. There, a combination of prepacking, pre-assembly, cross-docking and packaging management happens. This also limits the number of trucks the site has to deal with. Outbound handles the worldwide distribution of manufactured machines and ‘spares’.
This includes organising transport to the whole world (98% of production is exported) and managing the stock and logistics handling systems. Not only here, but also in the distribution centres and customer centres worldwide. We also manage the global supplier website for the Atlas Copco Group.
The GDC itself covers around 25,000 m². That is relatively small, but we have proportionally little stock because we work well with the suppliers to have short lead times. Still, it is starting to get too tight.
Is automation a solution to this bottleneck?
Absolutely. That is why we are going to install an AutoStore in 2024. That will allow us to ‘expand’. For us, this is the best way to stock parts: not only because such an installation takes up less space than, say, a shuttle system, but also because it is leaves back-ups. If one robot fails, another can easily take over its task. An AutoStore is the most interesting solution for our consumption profile.
“When we give training courses in Wilrijk, we regularly take our employees – worldwide – to Log!Ville to give them more insights.”
How important is innovation to Atlas Copco?
Very important, in the sense that it is one of our three core values, alongside ‘commitment’ and ‘interaction’. So our motto is: “There is always a better way”. Innovation is in Atlas Copco’s genes, both in terms of products and organisation, such as that of logistics. For example, we have been using Pick-to-Voice for years. Thirty years ago, we already had an automated warehouse for supplying the plants and ‘machining centres’ as well as AGVs for supplying components. We pioneered 3D Printing, VR glasses for training, you name it. We also own an active exoskeleton. So yes: we are very innovation-driven. By the way, that’s why we often participate in VIL projects. That way, we get a lot of concrete information first-hand.
In logistics, by the way, innovation is not always visible. A lot of optimisation is in the algorithms. They help to make the exact choices. What is the next order to pick? What is the optimal picking route? Which bin for which product? Which item to stock where? What is the optimal ‘lot size’? Which box to use when picking? Thus, the biggest optimisations and innovations are often not physically visible.
There is also visible innovation, such as the investment, together with Katoen Natie, in our first electric tractor. By the way, this is the first electric truck ‘Made in Belgium’ to roll off the production line at Volvo in Ghent.
Does that investment frame a broader sustainability trajectory?
Certainly: Atlas Copco is committed to reducing CO2 emissions from its own production by 46% by 2030, compared to 2019’s emission levels. This includes CO2 emissions from the entire value chain, including our customers. We want to reduce emissions from our suppliers and partners, such as transport companies, by 28% by 2030.
So in terms of sustainability, we also want to play a leading role. Components and machines are transported daily via multimodal solutions. To Turkey, we ship via shortsea. Inbound transport from Italy largely goes by rail. We also make very active use of inland navigation: almost all sea freight that leaves Airpower in Wilrijk goes via inland navigation to the port of Antwerp. Compressors and spare parts are transported to Willebroek, where they are then loaded into containers and sent to the port by barge via the Hutchison Ports Belgium terminal.
Investments are also being made in sustainable fuels such as HVO, bio LNG and Sustainable Aviation Fuel. SAF is a fairly new fuel and we want to gain experience. Through our partners, we want to trigger markets. By co-promoting and supporting these new technologies, they get the opportunity to develop faster. We are willing to pioneer in this. We want to be part of the solution for a better future.
Is that a reason why Atlas Copco Airpower became a supporting partner of Log!Ville?
That is indeed one of the reasons. So we can make Atlas Copco better known as an innovative company and pioneer. The innovative character of Log!Ville was also a reason: one can not only see different novelties in logistics in one place, but also see them in action. When we give training courses in Wilrijk, we regularly take our employees – worldwide – to Log!Ville to give them more insights in this area. For them, it is often not only a learning experience, but also an ‘eye-opener’.
How could Log!Ville add even more value?
By organising more lectures on innovations, during which users can share their experiences and experts can explain new developments. For example, we have tested RFID, but the accuracy was only 95%. For us, this is not good enough. Do other companies experience the same? And are there any ‘breakthroughs’ on the way? Such an exchange of experiences with novelties and information about updates could be an added value. There are plenty of topics on which companies can share their experiences and learn from. Some examples, chosen haphazardly: VR glasses, 3D printing, the AutoStore and you name it….
Log!Ville gives us inspiration to innovate faster. Thus, it helps us live up to our motto “There always is a better way”. Let Log!Ville be even more of a forum of ideas.