Kristof De Witte (WDP): ‘Buildings play crucial role in making logistics chain more sustainable’
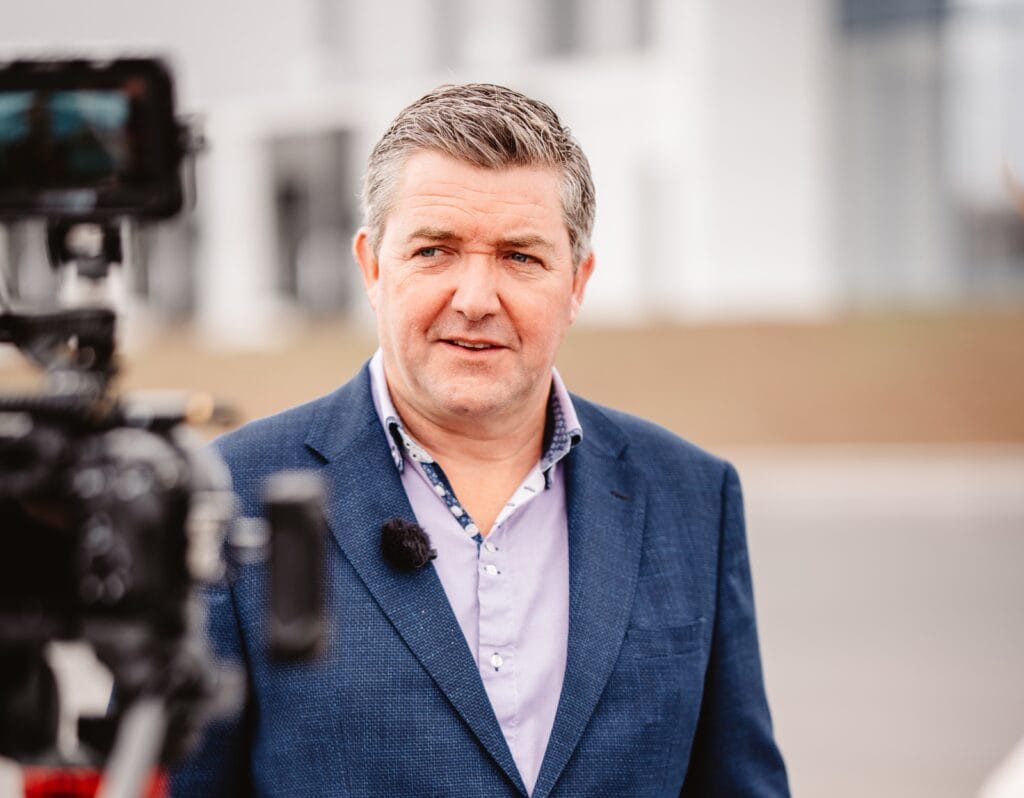
In the race towards climate neutrality, logistics companies are increasingly pressurised. European regulations – such as the Green Deal, the CSRD and the EU Taxonomy – are forcing them to act, but putting these into practice is extremely difficult. “Buildings can be greened fairly quickly. Transport is a different story. That requires a well thought-out strategy, in which buildings play a key role,” says Kristof De Witte, General Manager BeLux & France at LogiVille-Steering Partner WDP.
WDP recently published a white paper in which it provides logistics companies with tools to make their supply chains “future-proof”. The key message reads, “The time when sustainability depended largely on the sense of responsibility and market approach of individual companies is over. Today, it is a legal requirement. The EU is not yet on track to meet these legally binding targets. So a major shift-up in gear is needed”.
Sustainable transport is the biggest challenge
“Making logistics property more sustainable appears to be working well in practice. New warehouses are gasless as standard, equipped with heat pumps, LED lighting and high-performance insulation. They are also built higher. There are solar panels on the roof, which often produce enough energy to make the building even energy-positive,” says Kristof De Witte.
According to him, the real main breaker in making the supply chain sustainable is not the building but the transport. “This is and will remain the biggest challenge. Electric trucks are four times more expensive than conventional ones and have limited range. Many transporters are experimenting with it, but for now it remains at two trucks out of a fleet of 100,” he states. “Only in niches – short-distance shuttle traffic or last-mile in the city – e-trucks are profitable to use today.”
Buildings can make a difference in that transition, he argues. “Today’s warehouses are becoming small power plants. With batteries and electric vehicle charging stations, they are evolving into buildings that not only power themselves, but can also support the electrification of the customer’s fleet. We store solar energy during the day so that trucks can be charged at night. At a number of customers like Barry Callebaut in Lokeren or VDP in Zellik, we are already proving that it can be done.”
Still a long way to go
“Yet there is still a long way to go to decarbonise transport and meet European targets. The problem is that the regulations are not written specifically for the logistics sector, which makes the targets very difficult to achieve. And we are not just talking about the electrification of the truck fleet and automation that requires more energy, but also about the power grid that has to cope with the transition. In the Netherlands, there are already examples of new buildings that cannot be connected to the electricity grid. In Belgium, too, this is increasingly proving to be a problem,” says Kristof De Witte.
“We find, for instance, that Elia simply does not have enough engineers to do all the “grid studies” needed to cope with the increasing demand for electricity. Everyone is asking for extra capacity but there is none. Nor are the people to do the study work. We keep going round in circles like this.”
Existing buildings: the quiet work
Anyone who thinks sustainability is only about new buildings is mistaken. “Most of the logistics area is in existing buildings and these have to keep up. That is our biggest challenge, especially since there are few sites of a certain surface area available outside the port areas or along the Albert Canal. Existing buildings must therefore become more sustainable thanks to renovation, upgrading and renewal of installations. That work is less visible, but at least as important to make the supply chain future-proof,” he adds.
Opportunity or cost?
It is suggested in some circles that Europe is shooting itself in its own foot with the Green Deal and that sustainability targets should be revised downwards. There is therefore a chance that efforts to make the logistics chain more sustainable will weaken. However, Kristof De Witte nuances: “For major players and certainly the listed companies, sustainability is a strategic must. Pressure from shareholders and customers leaves no room for non-commitment. Banks also play a role: new financing is linked to sustainability requirements.”
However, even smaller logistics players should not expect to be able to adjust their targets. “You have companies that see opportunities in greening or even want to be best in class, but you also have companies that still see sustainability as a cost rather than an opportunity. You always have – as in other sectors – price breakers, who find it harder to pay for greening. They then try to implement or get their customer to accept a sub-optimal solution, but that too will only be temporary. If your customer is a Coca-Cola or a Unilever and has a sustainability strategy, as a supplier you must go along with this,” says Kristof De Witte.
So for him, the message is clear: anyone who does not have a sustainability plan will soon be off the table. “You don’t have to do everything perfectly right away, but you have to be able to demonstrate that you are working on it, and don’t forget the pressure of reporting requirements.”
Incidentally, the same applies to WDP itself. “We cannot just choose the cheapest contractor for a new building. They have to be able to demonstrate that they “source” their materials as climate-neutrally as possible. Where does their concrete come from? Is it produced sustainably? Not every company is as developed, by the way, as it requires a lot of documentation.”
From landlord to energy consultant (and provider)
So future-proofing the logistics chain and the energy transition involve enormous challenges. “The sustainability obligations are there, the logistics players often have the will and resources to take on the transition, but in a lot of cases the knowledge is lacking. Many logistics companies simply do not know where to start,” Kristof De Witte argues.
“As real estate players, our role is therefore changing profoundly. Whereas we used to offer square metres, today we are moving towards thinking along with energy solutions. Therefore, we are increasingly offering a total package that includes not only a storage building, but also proposals and solutions for decarbonisation of the vehicle fleet, solar panels, batteries, charging infrastructure, and so on.”
“So the customer doesn’t have to figure out how to install a battery or a charging station or have it subsidised by themselves, because we put those ourselves and we put those at the service of the customer. Like you fill up at a petrol station, you “fill up” at our charging station according to a pricing model that we have agreed together. In doing so, the customer chooses how flexible or fixed he wants his rates to be,” Kristof De Witte concludes.
Anyone wanting to know more about how logistics companies can make their supply chains future-proof will find further insights in WDP’s white paper on sustainable logistics. That also includes a handy checklist and four inspiring case studies. You can find the publication via the link below.
Want to know more about our Steering Partner? Discover WDP via this link.