Kristoff Van Rattinghe (Sensolus): “Tracking ‘assets’ allows us to optimise complex supply chains”
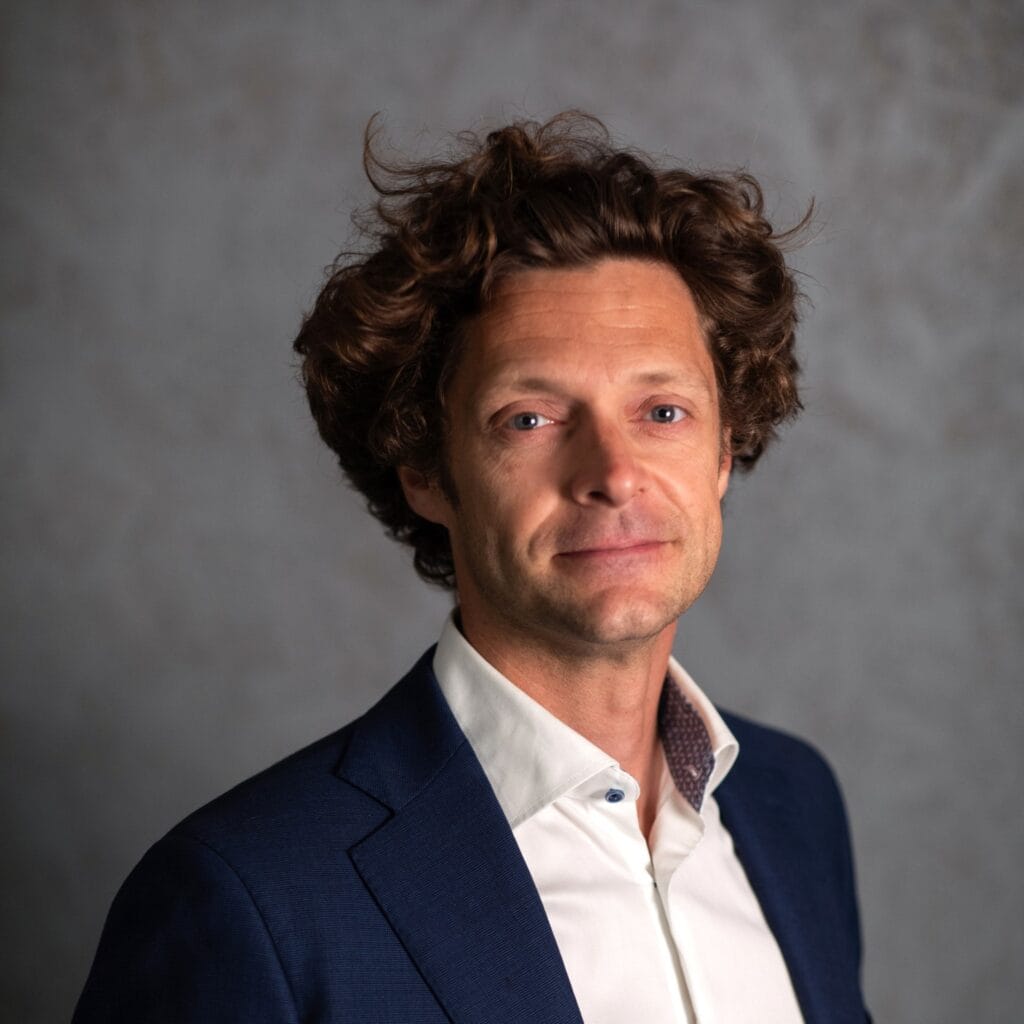
Kristoff Van Rattinghe (Sensolus): “By tracking “assets” Recently, Sensolus joined the LogiVille community as an Innovation Partner. The Ghent-based company specialises in tracking and managing mobile “assets” and more specifically load carriers such as reusable transport containers (RTPs), trailers, roll cages, crates, etc. Co-founder and CEO Kristoff Van Rattinghe introduces the company to us.
What is Sensolus and how did it come into being?
Sensolus was founded in 2013 and is based in Ghent. It specialises in digitising – non-motorised – mobile and industrial assets through Internet of Things (IoT) technology. With our solutions, companies can easily track and manage these assets, without the need for complex infrastructure or technical expertise. In doing so, we use sensors that are easy to install and last a long time without recharging.can optimise complex supply chains.”
Originally, we built sensors to better track seniors, but we quickly realised that the technology had more of a future in industry and logistics. 2016 was the year of the breakthrough when Airbus selected us out of 30 applicants to track critical parts worldwide with our IoT solution. Although Sensolus was really just a startup then.
Today, our company has some 55 employees – 40 of them in Flanders and the rest abroad. Besides Belgium, Sensolus operates in France, Germany, the UK, the Netherlands and the US, mostly with partner companies. Around 85% of sales are made outside Belgium.
Why did Sensolus choose logistics?
We discovered quite quickly that in logistics, the supply chain and certainly in manufacturing and retail, there are a lot of assets in use which, due to the fact that they are very mobile and constantly moving, are difficult to manage. We found that if we digitise their management, one can always know where they are and what they are used for. One can then also know how many are effectively used and whether more – or fewer – are needed. So this digitisation allows to improve deployment , optimise and better control the supply chain and reduce costs.
What do you mean by digitising load carriers?
Indeed, it sounds a bit peculiar when I say we are digitising the carriers. I mean: we hang a sensor on them, which allows us to know where the asset is, whether it is loaded or not, what the temperature is, whether there have been any shocks, and so on. Sensolus specialises in building the sensors and managing them.
We could use barcode scans or RFID, but these have their limits. They work best in closed loops, for example between two factories. I put two gates and all trolleys going in and out are scanned. In a closed loop, that works perfectly. But today’s supply chains are much more complex and mobile, so you don’t want to depend on those gates. With sensors, you have more freedom to measure and can gather data without scanning. That data goes directly to a platform in the cloud.
So you can track many more assets accurately. One of our big customers, as mentioned, is Airbus, for which we monitor 25,000 parts today. We know where they are at all times, in which country, with which subcontractor.
Today, we have already digitised more than1 million assets that we can track. That data is generated without anyone having to scan anything. All those pallets, containers or trolleys become fully visible in the chain.
How do you gather that data? With a GPS?
The sensor can be connected to a GPS, but actually we use different technologies depending on the type of carrier or deployment. Outdoor, it can be a GPS signal or indoor, a Wi-Fi signal. We also use bluetooth. You are not going to track a trolley, for example, by GPS because they are either in a warehouse or in a truck and so no signal can be transmitted. For this, bluetooth tags are more appropriate. They are cheap and easy to use.
Nowadays, you have people hanging bluetooth tags on their suitcases or keys. We do the same, but on an industrial scale. So we can easily track 20,000 rolling carts and know how they are used. How many are in rotation? How many are stationary? Where are some still available? That is the added value we bring: thanks to that data, we optimise the fleet of load carriers.
Which carriers do you digitise the most?
Those are the JIGS, customised load carriers that are very often used in the automotive and aerospace industries for transporting parts. They represent the largest share in our overall portfolio.
But technology is evolving so fast, and the price of sensors is falling so fast, that trackers can today be plugged into a wooden pallet with a favourable ROI. For companies specialising in renting out reusable pallets, this is particularly interesting because many of those carriers are lost throughout the supply chain. That chain is so globalised and so many subcontractors are used due to outsourcing that you often don’t know where the pallets are anymore. With our technology, you regain control of those assets. And here, too, the added value lies in better management of them.
Aircraft parts are very expensive, so the price of a tracker plays a small role. For a roll cage costing a few hundred euros, the situation is different. As the price of trackers drops – and the functionalities become broader – that opens up opportunities for many more carriers than before.
What are the next steps for Sensolus?
As I said, trackers can achieve a favourable ROI even with cheaper load carriers and assets. We are in the automotive and aerospace industries today, but there are millions of carriers that are not yet digitised and connected. We also see that, partly due to legislation and the Packaging and Packaging Waste Regulation (PPWR), more and more companies are using reusable packaging. Many smaller mid-market companies also need to make the move.
For foldable crates in retail, the technology is still a bit too expensive. Indeed, you have not only the cost of the tracker but also the monthly cost of follow-up. After all, we sell our technology as a service. For the more expensive assets in small volumes, we talk about 5 or 6 euros per month per asset “all-in”, but for roll containers we talk about amounts under 1 euro. So for the time being, we cannot offer this service profitably for, say, crates in which tomatoes are transported to a supermarket. But in time: “who knows”?
Finally: what appealed to you to become a LogiVille partner?
As Sensolus, we started in industry and its supply chain, but soon ended up in logistics in general. Logistics is a sector where different parties have to work together. And that is why it is very interesting for us to have those conversations with all those parties, to hear their needs, to see what the trends are in their segment, what complex challenges they are experiencing.
Especially since Covid, a lot of changes have happened in supply chains and the related ecosystem. Therefore, it is important for us to know what the needs of the industry are. LogiVille is a kind of “learning network” for us. We want to know what the pain points are in the sector so that we can find and apply solutions. We are very good at building solutions, but you cannot “build to build”. That is of no use to the companies – and also to us.
On the other hand, it is important for logistics companies to know that we can provide solutions to optimise their supply chains and processes. So thanks to LogiVille, we learn from them and hopefully vice versa.
Keen to find out more? Sensolus is hosting a webinar around “Asset tracking in Transport & Logistics” on Thursday 26 June, presenting concrete use cases from a number of customers. These include DHL & Deutsche Post, Ampère (sphere), DPD Fresh and ABInBev. More info can be found on the Sensolus website.
The Future of Work
Sensolus is also part of the new Thematour “The Future of Work”. This Thematour, with seven new partners, offers a unique insight into how digitalisation, automation and Artificial Intelligence (AI) are shaping tomorrow’s workplace. In addition, the changing expectations of a new generation of workers, such as Gen Z, play a crucial role in the future of work.
Get inspired by hands-on demonstrations and innovative applications from leading partners and discover how your company can be ready for “The Future of Work”!