Marc Meuris (Enfoil): ‘Flexible and robust, customised PV-film opens up new opportunities in logistics’
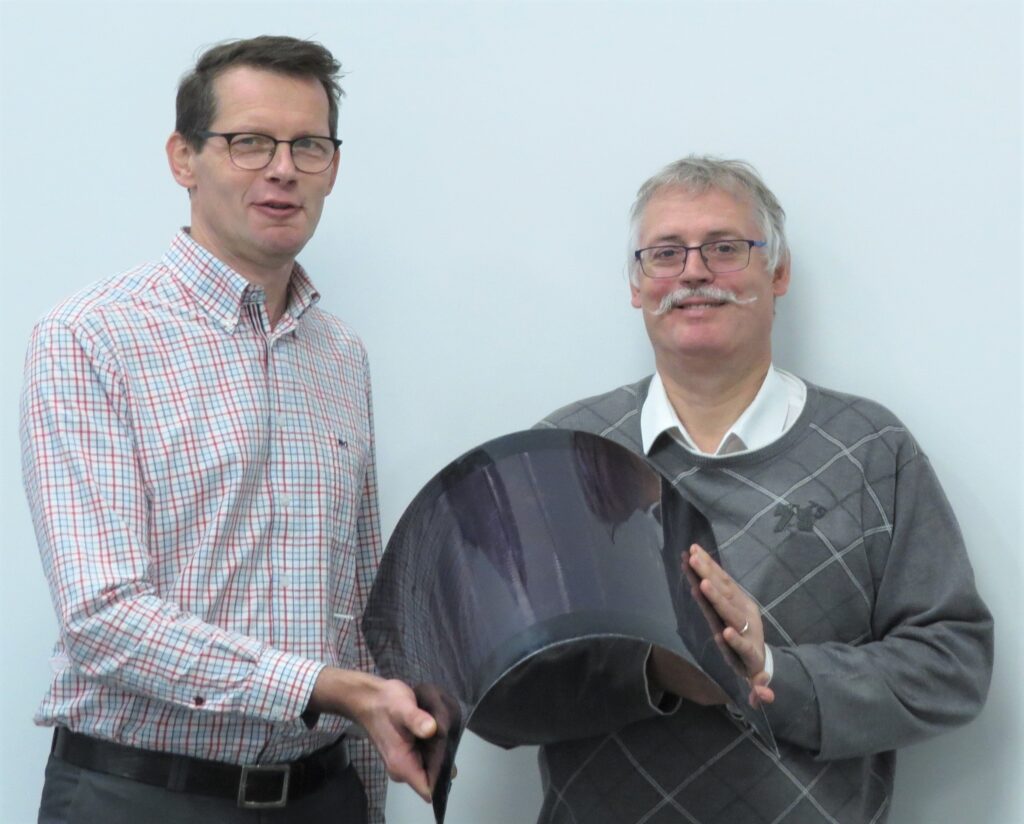
At the beginning of June, Start2Scale-up Avenue added another partner to their ranks with Enfoil, a developer and manufacturer of photovoltaic film which can be used in the logistics sector and other areas. The film is flexible and robust and can be easily customised, offering endless opportunities. ‘Log!Ville is sure to help us identify a range of applications we had never even considered,’ says CTO Marc Meuris (right in the photo).
How and when was Enfoil created?
Enfoil is a spin-off of Solliance, a Belgian/Dutch collaborative venture that was started in 2010 by imec, UHasselt and TNO. It aimed to develop thin and flexible PV cells, the technology to interconnect them and the ‘mass customisation’ manufacturing process. As of this moment, that technology is mature, readily available and the film can be commercialised. So, Enfoil was founded just under a year ago. We are based at the EnergyVille campus at Thor Park in Genk and, in the long-term, we are planning to be active in Eindhoven. The driving forces behind this venture are CEO Dominique Coster (left in the photo), COO Bart Van Winkel and me as CTO. I have worked as a programme manager at imec for 30 years, 14 of which were within Solliance.
What is the difference between a classic solar panel and the PV film from Enfoil?
The biggest difference is that a classic solar panel is made using a crystalline material and CIGS film (Copper, Indium, Gallium and Selenium). A traditional PV panel has an efficiency level of around 21% and our PV film is not far off that figure (17%). The film is not only thinner (just 2-3 mm thick), lighter (2 kg/m2) and flexible (with a radius of 10 cm), but also more robust (it can even be walked on). The production process is also around 60% more CO2-friendly.
So, how does Enfoil film differ from other PV films?
PV films are not unique but they tend to be produced in standard sizes. The major difference here is that the size of our film can be customised both in length and width and, because the lengths can be connected easily, rolls can be customised to any size. We also realise an efficiency of 17% while some thin film solar panel variants only achieve 10-12%, as they are based on organic materials.
Is Enfoil’s PV film market-ready?
Yes, partly thanks to the fact that we have developed a method within Solliance for large-scale manufacturing, using a ‘mass customisation’ process. As a result, we are now working in parallel on commercialisation and starting up production. This will initially take place with TNO in the Netherlands, where a prototype of a ‘mass customisation’ production line is being created. At 10,000 m² per year, its capacity is enough for the market validation process concerning both the technology and the business cases for the various applications. We will then scale up and create our own production unit which will offer a capacity of 100,000 m² or potentially even 200,000 m² per year.
Which markets are you targeting?
primarily, the logistics and e-mobility sectors. From that point on we will focus on applications where the ability to roll up and roll out the film offers advantages, such as temporary applications in the field. A third market could be roof tiles. Flat PV roofing tiles already exist but there are no ‘traditional’, curved tiles. This market, however, is proving to be more difficult than expected, as the building sector is very conservative.
Are you already using this technology in logistics?
For a large logistics service provider, we provided customised PV strips which were installed on an ISO container between the roofing ribs. The generated electricity is used to provide continuous power to a battery for the monitoring and track & trace systems. Until then, the battery had to be charged up every eight days. In this setting, the robustness of the film is of great significance because containers are often handled quite roughly during transshipment processes.
Another application we are working on is the installation of PV film on the roof of electric delivery trucks; flexibility is a significant factor in this setting to support the vehicle’s battery and increase the action radius or decrease the charging cycle.
PV films can also be installed on the roof of refrigerated trailers in order to support the cooling unit’s battery by providing more power. Unfortunately, it is not yet possible to supply the unit entirely using PV power.
Another potential application is the combination of a battery-electric tractor and a trailer covered in PV film. The power would increase the driving range of the vehicle by 5-10% but, unfortunately, current legislation only allows power to flow from the tractor unit to the trailer and not the other way around. We expect this to change soon, however.
Why did Enfoil become a partner of Log!Ville?
We believe there are many more applications in logistics for us to discover and, by connecting with other partners and visitors, we aim to find new, beneficial routes. Someone who notices how we apply the strips to a container, for example, may have an idea for a similar solution in another area.
Our presence at Log!Ville allows us to expand our understanding of the logistics sector and also show businesses that they can count on Enfoil to develop new applications.
We are on the cusp of a substantial transition to electric mobility and businesses have masses of questions and challenges. Brainstorming with them gives us a chance to find out how we can help or, if necessary, offer additional expertise. Thanks to our base at EnergyVille, we also have a broad network of businesses that are leading the field when it comes to energy development. We are, therefore, not only learning but also providing advice.
In other words, thanks to Log!Ville, we are able to create various interactions.