Filip Peeters (Nike): “Increasing flexibility of logistics workers is a necessity, and a challenge”
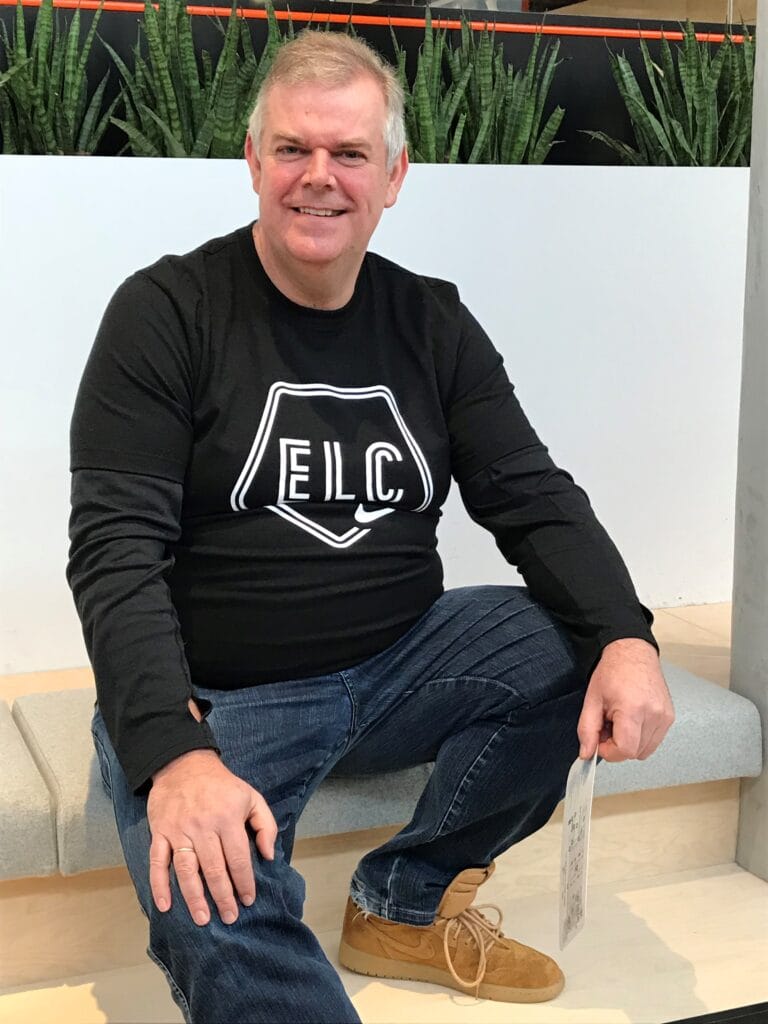
Nike’s European Logistics Campus (ELC) in Laakdal is considered a flagship of logistics in Flanders. Among other things, it stands out for its progressive human resources policy with a focus on diversity, inclusion and creating an attractive working environment with career opportunities. Together with human resources manager Filip Peeters, we look at how the ELC is adapting to the evolution of the labour market and how the logistics sector can make jobs more future-proof.
Nike’s European Logistics Campus (ELC) consists of five neighbouring distribution centres in Laakdal, Meerhout and Ham with a total area of 465,000 m². It serves over 40 countries in Europe, the Middle East and Africa with sportswear and footwear. Its customers are wholesalers, its own Nike shops and e-commerce customers.
‘In total, we have around 6,000 employees. They work in three shifts (early, late and night) processing the biggest volumes and, on weekends, in two shifts (from 6am to 6pm), for urgent and time-critical orders. Until about two years ago, we sometimes struggled to find new staff quickly enough. Currently, we are not looking for new permanent staff except for bottleneck profiles. Indeed, two years ago, the labour market was completely ‘dry’ which we compensated by investing heavily in automation. This means that we can now handle more volumes with the same number of people,’ explains Filip Peeters.
Nike previously automated cardboard-based stocking, but now the focus is on packaging automation, which is the most labour-intensive activity. ‘First, we implemented it for shoes and now also for apparel. With growing ‘dot.com’ orders, our cost per unit is rising. A carton of seven different shoe boxes for one customer requires relatively little work per unit. E-commerce orders are more fragmented and their packaging is therefore more labour-intensive. Thanks to the automation of that activity, the logistics cost per unit drops faster.’
Increasingly switching to techinally educated staff
Due to automation, there is a growing need for more technically educated staff. So a challenge for us was to make our own people ‘future-fit’ and train them,’ Peeters adds. ‘A second big evolution is that we are moving more towards real-time systems for planning. Software organises scheduling differently, in the sense that orders are now offered in ‘batches’ of an hour. The coordination of batches thus becomes more important than the scheduling itself’, he adds.
Providing career opportunities
Despite automation and a relative decline in staff shortages on the Antwerp/Liège axis due to the cooling economy, he says the search for logistics talent remains a concern. ‘That is why we stick to the principle we have been using for 30 years, in particular that an interim worker can progress to a temporary contract and then a permanent contract. So we place great emphasis on a sophisticated internal learning path. On top of that, many employees are often hungry for new challenges. By giving them opportunities to learn new things and broaden their experience, we can offer them variety in jobs.
For example, getting them to work first in the ‘first mile’ (bringing in the goods), then in the ‘outbound’ (the next link in the supply chain), and subsequently in distribution (the route the finished product takes from the warehouse to the end consumer),’ Peeters adds.
Training serves not only to advance within the organisation, but also to make tasks more flexible. This also allows employees to shift temporarily to time-critical activities, for example. ‘In one of the five distribution centres, it can sometimes be busier than usual. In the past, we often had to handle these peaks with temporary workers. Today, we have the luxury of being able to shift people from one distribution centre to another as we simplified and increasingly standardised processes. The flexibility and deployability of our employees is a competitive advantage’, Peeters stresses.
‘Artificial intelligence will accelerate the trend towards automation of many tasks – such as scheduling. ‘So you have to make sure that you allow both jobs and profiles to evolve with you.’
Flexible deployment of staff
He says more flexible deployment of in-house staff is an industry-wide trend. ‘Of course, it is not easy to deploy forklift drivers for ‘order picking’ or packaging. Nevertheless, logistics companies should pay more attention to making their staff more multifunctional, and thus training and standardising processes within the organisation.’
‘But employers also need to show more flexibility to future-proof work in logistics’, Peeters says. They should not take action on structures and work design, but also be more flexible so that employees can evolve with them. Artificial intelligence will accelerate the trend towards automation of many tasks – such as scheduling. ‘So you have to make sure that you allow both jobs and profiles to evolve with you.’
‘Automation in the past was meant to take over ergonomically demanding tasks. That battle is now over. Today, automation serves more to take over simple and less attractive tasks, so that value-added tasks can be entrusted to employees. It is important to involve employees in this process and ensure that their job remains engaging,’ he says.
‘Why do people come to work? The three main reasons, studies have found, are: for the money, for the social contact opportunities and to make a positive contribution where they can make a difference. So as an employer, it is important that employees can combine a team spirit with meaningful and varied work’.
Allowing paradigms to evolve
To achieve this, paradigms need to change. The logistics sector tends to be quite conservative. So the challenge is not only to get employees on board, but also for the sector itself to evolve. ‘Today, job content defines which category someone belongs to and according to which scales they are paid. So the question is whether this system is future-proof if people want to organise work more flexibly and with more variety. It will not be an easy exercise, but within the sector we should already dare to think about it with the social partners,’ says Peeters.
This exercise is all the more important because staff shortages are structural and the use of innovation and automation will increase. ‘Technology is evolving rapidly and becoming increasingly cheaper. As a sector, we must therefore ensure that the paradigms and human factors also evolve with it’, he stresses in conclusion.
The Future of Work
From March 11th to June 26th, 2025, LogiVille will be dedicated to ‘The Future of Work’. It offers a preview of how work is changing and the role of technology, sustainability and new ways of working together.
This theme provides an insight into the challenges and opportunities for companies and professionals in the logistics sector and supply chain.
Read more and book your tour now!
Supporting partner
Want to know more about this Supporting Partner? Discover everything about Nike via this link.